Safety and Innovation at the Forefront
Safety and Innovation at the Forefront Nylacast Automotive's Impact on EPS (Electric Power Steering) Systems
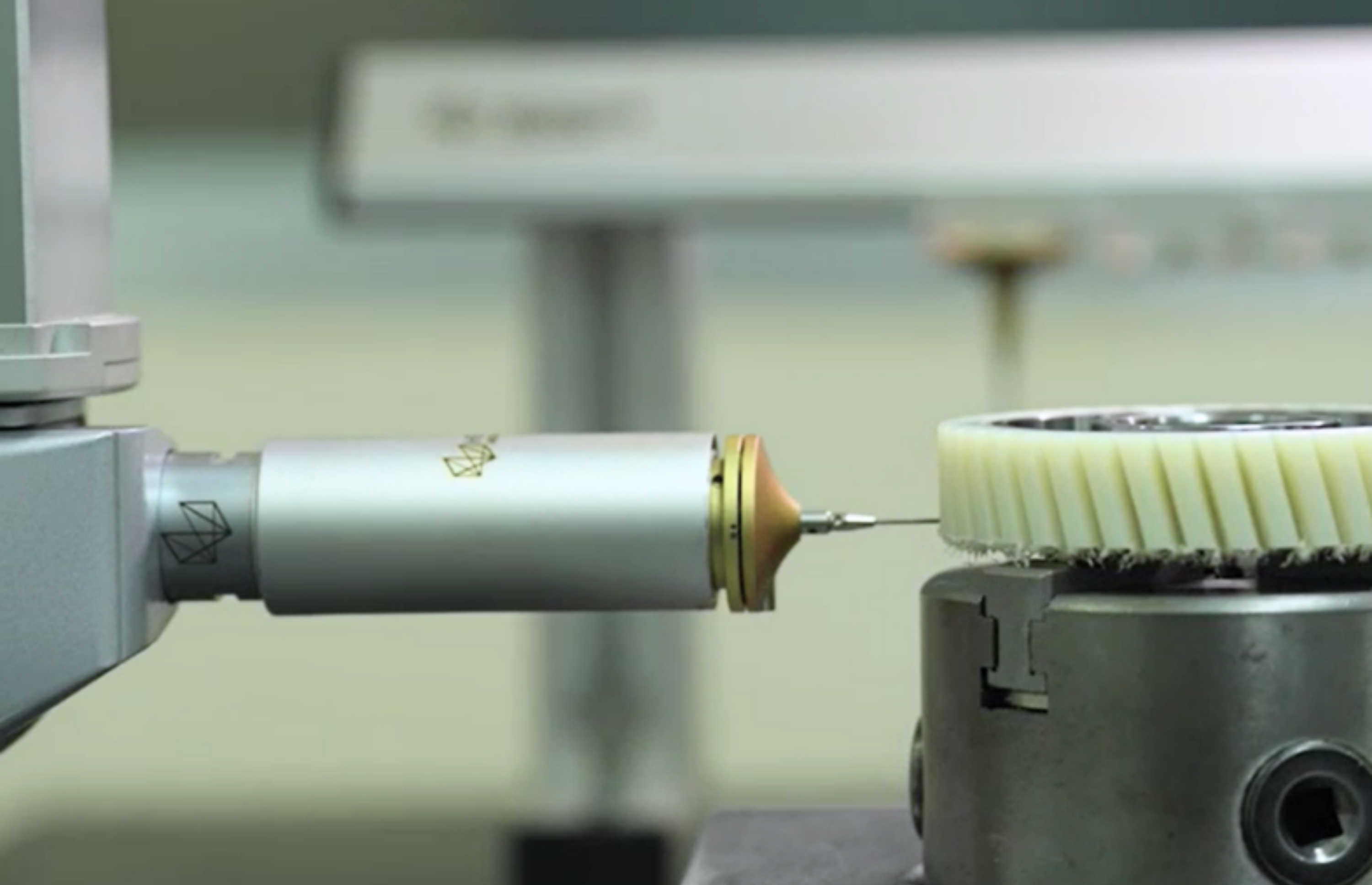
In the EPS system, every component plays a crucial role in ensuring driving safety. Nylacast Automotive, as a professional worm gear supplier, are well aware of the critical role our products play in ensuring vehicle safety. Worm gears, as an indispensable part of the EPS system, not only perform basic physical functions but also enhance the performance of the steering system and driving experience. Their high performance ensures precise response and stable operation of the system, making them a key component of driving safety. Therefore, in the design and manufacture of worm gears, we always prioritize safety, ensuring that each product meets or even exceeds industry standards.
How does Nylacast Automotive ensure the safety-critical performance of worm gears?Nylacast Automotive is a leading Full-Service Supplier, specializing in offering high-performance worm gear solutions for the automotive industry. By integrating advantages across the following key areas, we ensure that the safety-critical performance of our worm gears is fully guaranteed:
- Customised polymer formulation development: Tailored to specific customer needs, we develop customized polymer materials with low friction coefficients, high strength, high torque, wide temperature performance ranges, and long lifespans. Our solutions offer low noise, wear resistance, and lightweight benefits, ensuring long-term stable operation of worm gears and enhancing vehicle safety.
- Advanced casting processes: Nylacast Automotive employs in-house formulated casting processes that produce cast co-polymer products with low internal stresses and thermal mechanical stresses, ensuring the durability and safety of critical components like worm gears under various environmental conditions. The core feature of the process is that it produces a virgin material, where the basic raw materials are carefully mixed in specially developed machines, the liquid being poured into special tools where the polymerization reaction takes place. Casting process advantages:
- Low internal stresses: Molecular chains are not oriented by force, resulting in no internal stresses.
- Minimal thermal mechanical stresses: Avoids melt disturbance and large temperature gradients.
- Superior physical properties: Specially formulated cast co-polymer products have high strength, good toughness, and excellent damping performance.
- Enhanced durability: High molecular weight characteristics ensure a long lifespan.
- Polymer-to-metal bonding and precision tooth cutting technology: Our Automotive Division's technological strengths are not only reflected in the production processes of raw materials but also in polymer-to-metal bonding and worm gear tooth cutting technology.
- Polymer-to-metal bonding: Through innovative processes, the polymer is tightly bonded with the metal hub, enhancing bond strength, optimizing heat dissipation, ensuring stability at high temperatures, and boosting the safety of worm gear operation.
- Precision tooth cutting: Using "hobbing" technology to manufacture gear teeth with high precision, improving service life and NVH performance, meeting automotive industry safety.
- Precision tooth profile design: Working closely with customer engineers, we ensure each gear design precisely meets technical requirements. We actively optimize gear designs through lightweight and high-performance material selection, enhancing transmission efficiency and safety.
- Performance Optimization: Gear profile, diameter and width are optimized through careful parameter tuning, combined with worm shaft machining, all for optimal torque output, durability, and NVH performance.
- Lightweight & Compact: Reducing size and weight to provide greater flexibility in vehicle mounting space and improve energy efficiency.
- Advanced analysis and validation: Part design review and optimization through international design guidelines (VDI 2736, KISSsoft embedded) and Finite Element Analysis (FEA) analysis.
Tooth contact Analysis
Comprehensive testing and verification: Nylacast conducts comprehensive testing and verification of materials and products according to international standards such as ASTM, ISO, and IEC, as well as specific test specifications from customers. Simulating various extreme conditions, we assess the durability and load-bearing capacity of worm gears, ensuring safety performance under extreme conditions. Testing includes Pull-off / Knurl adhesion, Axial push-off, ultimate interface torque, ultimate tooth torque, and worm and gear verification.- Quality assurance: Besides ensuring all developed materials and products pass stringent quality control processes to meet or exceed customer expectations and industry safety All our employees must undergo rigorous training programs to understand and implement our quality standards.
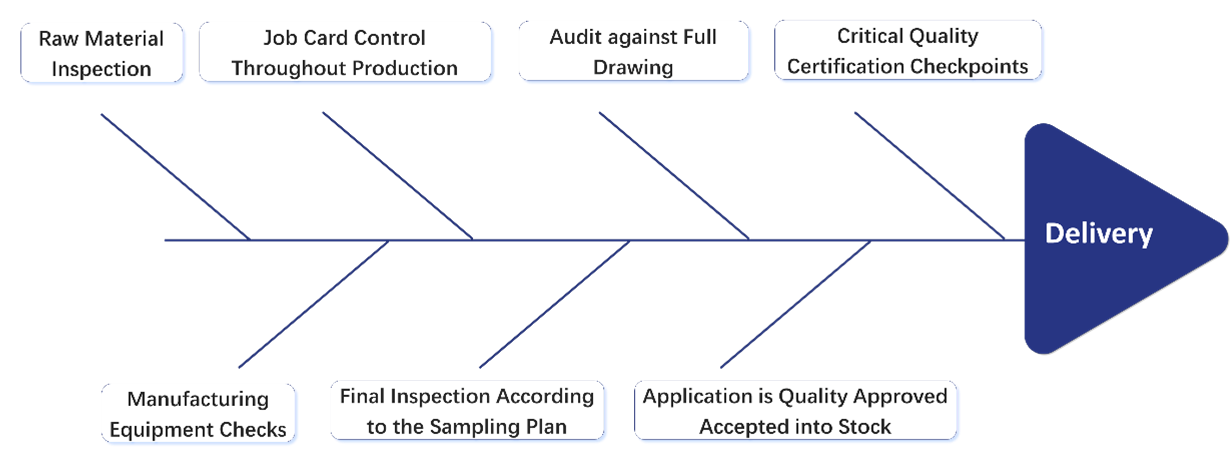
- Optimisation and innovation: Through continuous R&D activities, we optimise the performance of existing materials and products while exploring new innovative pathways to enhance product safety Our "cast polymer products" are widely used in C-EPS, SP-EPS, DP-EPS, and have been successfully applied to Steer-by-Wire (SbW) EPS platforms.
Evaluation – A Testament to Trust and Recognition
We are extremely proud to share the positive feedback we have received from our customers. These evaluations are not only a recognition of our work but also a motivation for us to continuously improve: "Your worm gear products have significantly enhanced the performance and reliability of our EPS systems.", "Thank you for your company's professional service and high-quality standards, we have noticed a significant reduction in defect rates in the finished products."
CEO of Nylacast Automotive, Simon Harvey: "The safety and quality standards we are committed to have been perfectly embodied in providing solutions for EPS applications. Every effort made by the company is to meet or even exceed customer expectations."
Conclusion
Through precision casting processes, comprehensive testing capabilities, stringent quality assurance systems, and proactive R&D innovation, Nylacast Automotive's worm gears provide a solid safety foundation for EPS systems. As a Full-Service Supplier, we are committed to continuously improving our products to ensure they perform optimally. Choosing our worm gears means choosing trust, safety, and advancement.