Advanced Nylacast Polymer Casting Technology
Redefining New Standards in the High Precision, Safety Critical Automotive Polymer Gear Industry
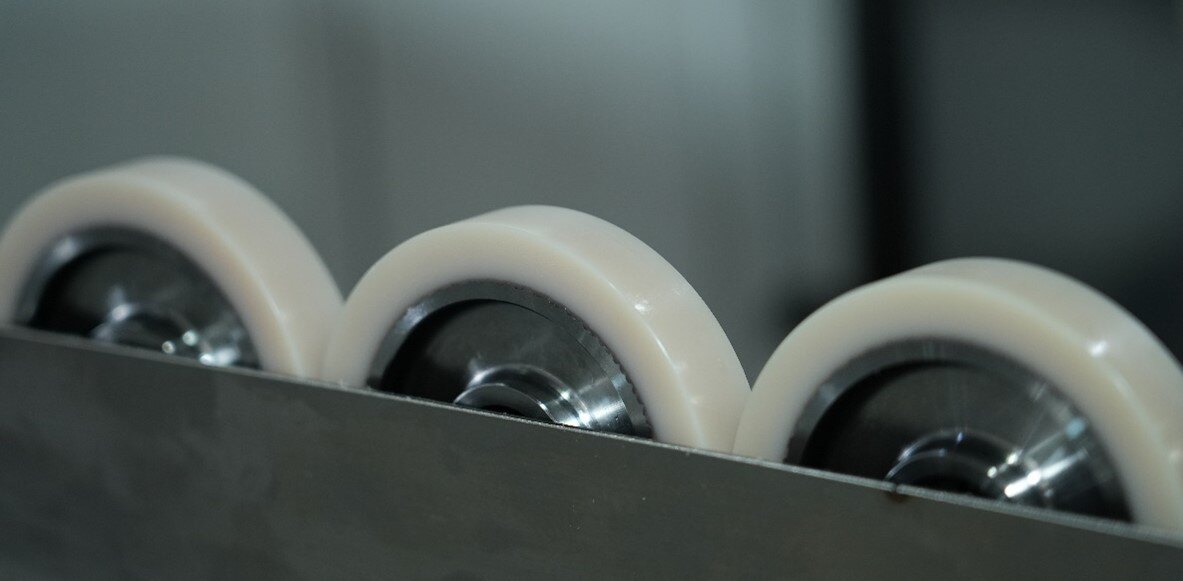
Background
Nylacast Automotive is a global-leading designer and high volume manufacturer of high-precision, safety-critical polymer components. Our current business areas include Automotive EPS systems, braking systems, actuators and transmission components.
Nylacast polymers are specially formulated for automotive safety-critical applications to exhibit excellent physical properties including high wear and fatigue resistance, dimensional stability, and excellent NVH performance through its unique Nylacast Polymer Casting Process, as the final polymer chemistry displays ultra-high molecular weight and long-term (durability) performance.
The Nylacast Polymer Casting Process using our own in-house chemistry and equipment, which is optimized for polymer gears and has been refined over more than 25 years, we produce polymer materials with higher molecular weights and improved durability, exhibiting exceptional physical properties:
- High wear resistance,
- Enhanced dimensional stability,
- Low wear rates,
- Improved NVH performance.
Advantages of Nylacast Casting Technology Nylacast 浇铸技术的优势
Nylacast designs and develops co-polymers by the controlled polymerisation reaction of raw chemicals in centrifugal casting tools, resulting in a virtually residual stress-free polymer with high crystalline structure (improved strength and stiffness) and ultra-high molecular weight.
These are the key characteristics for applications requiring excellent mechanical fatigue and surface wear resistance. Therefore, Nylacast Casting Technology demonstrates significant advantages in the production of automotive polymer-metal gears.
Key Features of Nylacast Cast Polymers – Ultra-high Molecular Weight Nylacast
The molecular weight is a key feature of for polymer-based components subjected to cyclic loads, i.e., mechanical fatigue, directly affecting the performance under real field conditions:
- Enhanced Durability and Service Life: Longer molecular chains and narrower molecular lengths distribution ensures structural integrity over long-term use.
- Improved Damping Performance: The increased number of interactions among ultra-long molecular chains enhance the kinetic friction between molecules and, therefore, vibrational and impact energies are absorbed more efficiently, lowering noise and vibration levels.
Solving Pain Points in the Automotive Polymer Gear Industry: Nylacast Casting Process Enhances Polymer Gear Performance
- Increased Wear Resistance: Polymer gears produced by traditional injection molding processes are prone to wear, leading to increased maintenance costs and shortened lifespan. The unique Nylacast Casting Process enhances the morphology structure of the polymer (e.g., ultra-high molecular weight, high crystallinity levels), maintaining good condition even under high cyclic loads and prolonged operation, extending the lifespan (durability) of the entire system.
- Enhanced Dimensional Stability: Parts made by traditional injection molding methods often deform under high temperatures or heavy loads. Nylacast Casting Technology and superior machining techniques, guarantees a product with extremely high geometric precision and dimensional stability even under extreme temperature variations.
- Reduced Noise and Vibration (NVH): Combining the strengths of metals and the durability and dampening characteristics of polymers, the Nylacast Casting Process delivers products (EPS polymer-based gears) with mechanical robustness, durable, and excellent dampening and noise reduction characteristics.
- Better Frictional Properties: Chemical additives in the Nylacast Casting Process are fewer and typically added in liquid form, reducing interference with the material structure, resulting in better friction attributes.
- Customized Solutions: Leveraging extensive design and development experience and strong R&D capabilities, we can tailor exclusive solutions based on specific customer requirements, whether for specific tribological conditions or thermomechanical performance requirements.
Customer Testimonials
"We chose Nylacast not only for their product quality but also for their innovative capability and service awareness. Nylacast Casting Process has shown us many possibilities."
"Nylacast Casting Technology provided us with a brand-new solution, addressing multiple challenges we encountered in high-performance steering systems."
"In the electric vehicle domain, Nylacast Casting Technology helped us overcome many technical challenges, especially in noise and vibration control."
CEO's Comments
"As the CEO of Nylacast Automotive, I know that Nylacast Casting Technology delivers multiple key performance advantages to our customers addressing NVH, Durability and High Torque carrying capacity. This technology not only represents our leadership position in the field of material science but also reflects our deep understanding of customer requirements and our ability to respond quickly." It’s really interesting to see the number of enquiries coming in from both Tier 1 assemblers and the OEMs into our Application Engineering and R&D functions relating to these 3 challenges — Simon Harvey
By adopting state-of-the-art technologies either in polymer engineering & science (Nylacast Casting Technology) as well as in precision manufacturing, Nylacast Automotive is continuously and successfully addressing multiple industry pain points in safety-critical and high precision automotive polymer gear applications, providing customers with more reliable and efficient solutions. This continues to strengthen our relationships with customers and confirms our best-in-class reputation within the industry.